En un entorno industrial cada vez más orientado hacia la sostenibilidad, la forma en que se gestionan los activos y se planifica el mantenimiento puede marcar la diferencia. El mantenimiento sostenible no solo busca minimizar el impacto ambiental, sino también maximizar la eficiencia operativa, reducir los costes y prolongar la vida útil de los equipos.
En este artículo, detallaremos cómo implementar un plan de mantenimiento sostenible paso a paso, qué indicadores utilizar para evaluar su eficacia, qué prácticas son recomendables y por qué el reacondicionamiento de equipos es una pieza clave en este enfoque.
1. ¿Qué es un plan de mantenimiento sostenible?
Un plan de mantenimiento sostenible es una estrategia estructurada que permite mantener en condiciones óptimas los equipos industriales, reduciendo al mismo tiempo el consumo de recursos, los residuos generados y el impacto ambiental global. No se trata solo de reparar averías, sino de anticiparse, optimizar y reutilizar.
Sus pilares son:
- Prevención frente a corrección.
- Uso eficiente de materiales y repuestos.
- Priorización de la reparación sobre la sustitución.
- Monitorización de indicadores clave de rendimiento (KPI).
- Incorporación del reacondicionamiento como práctica habitual.
2. Pasos para implementar un plan de mantenimiento sostenible
Paso 1: Diagnóstico inicial de activos
Antes de establecer un plan, es fundamental conocer el estado actual de los equipos:
- ¿Qué activos presentan mayor desgaste?
- ¿Cuáles tienen mayor tasa de fallo?
- ¿Cuánto cuesta repararlos o reemplazarlos?
Este análisis permitirá decidir qué equipos pueden ser sometidos a reacondicionamiento en lugar de ser reemplazados.
Paso 2: Clasificación de criticidad
Ordenar los equipos según su impacto en la operación:
- Alta criticidad: parada de planta o riesgo de incumplimiento normativo.
- Media criticidad: afecta la producción, pero permite continuidad parcial.
- Baja criticidad: no compromete la producción.
Esta clasificación guía las prioridades de mantenimiento y reacondicionamiento.
Paso 3: Definición de KPIs
Algunos indicadores clave para evaluar el plan:
- MTBF (Mean Time Between Failures): tiempo medio entre fallos.
- MTTR (Mean Time to Repair): tiempo medio para reparar.
- Disponibilidad (%): proporción del tiempo en que el equipo está operativo.
- Ratio de reacondicionamiento vs sustitución.
- Consumo energético asociado a mantenimiento.
- Residuos industriales generados por intervención.
Paso 4: Diseño de acciones preventivas
Establecer una programación periódica de revisiones, lubricaciones, cambios de piezas, ajustes…
Evitar fallos antes de que ocurran es más sostenible que reaccionar ante averías.
Paso 5: Integración de reacondicionamiento de equipos
Aquí entra en juego una de las decisiones más sostenibles:
Reacondicionar un equipo consiste en devolverle su funcionalidad original mediante la revisión, reparación o sustitución de componentes críticos, manteniendo la estructura base.
Ventajas:
- Menor coste frente a sustitución.
- Reducción de residuos industriales.
- Ahorro energético en procesos de fabricación.
- Rapidez frente a la compra de equipos nuevos.
Por ejemplo, reacondicionar una bomba de vapor puede suponer un ahorro del 40 % en costes y una reducción del 60 % en residuos generados.
Paso 6: Formación del personal técnico
La sostenibilidad también depende del factor humano. Un equipo formado en buenas prácticas de mantenimiento sabrá identificar oportunidades de mejora, ejecutar intervenciones con menor impacto ambiental y reconocer cuándo optar por reacondicionar en vez de reemplazar.
Paso 7: Digitalización y trazabilidad
El uso de herramientas de gestión de mantenimiento (GMAO o CMMS) permite:
- Registrar intervenciones y piezas utilizadas.
- Automatizar alertas para mantenimiento preventivo.
- Controlar el estado de reacondicionamiento de equipos.
- Generar informes sobre KPI sostenibles.
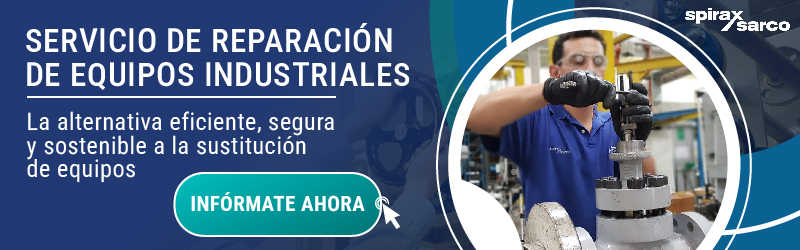
3. Buenas prácticas para un mantenimiento sostenible
- Priorizar piezas reacondicionadas certificadas sobre repuestos nuevos.
- Trabajar con proveedores que ofrezcan servicios de reacondicionamiento en lugar de venta directa.
- Almacenar piezas críticas reacondicionadas para minimizar tiempos de parada.
- Definir un protocolo de decisión para determinar si un equipo se repara, reacondiciona o sustituye.
- Colaborar con talleres externos especializados que garanticen calidad, trazabilidad y garantía en los equipos reacondicionados.
4. El papel estratégico del reacondicionamiento de equipos
El reacondicionamiento de equipos ya no es solo una opción táctica para ahorrar en una emergencia. Es una decisión estratégica para empresas que desean:
- Cumplir con objetivos de sostenibilidad (ESG).
- Obtener certificaciones ambientales como ISO 14001.
- Mejorar su rentabilidad operativa.
- Responder a auditorías con datos reales de impacto ambiental reducido.
Al incluir el reacondicionamiento como práctica sistemática en el plan de mantenimiento, las empresas no solo reducen costes, sino que posicionan su marca como responsable y eficiente.
Implementar un plan de mantenimiento sostenible no es solo una cuestión técnica, sino también estratégica. Las organizaciones industriales que adoptan este enfoque reducen su impacto ambiental, mejoran la eficiencia de sus operaciones y ahorran significativamente a medio y largo plazo.
El reacondicionamiento de equipos se presenta como un aliado clave en este modelo, permitiendo mantener la fiabilidad de los activos, reducir residuos y avanzar hacia una economía circular dentro del entorno industrial.
¿Está su empresa preparada para dar el siguiente paso hacia el mantenimiento sostenible?marcha la operación, sino que también garantice un futuro más limpio y competitivo.
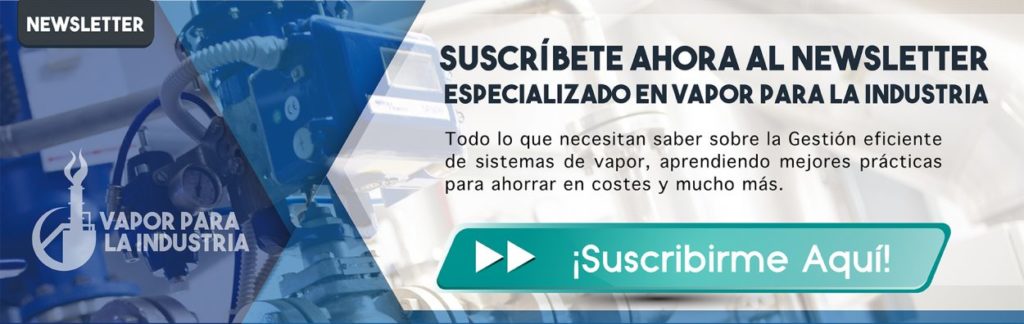
Deja una respuesta