Apresentamos aqui um caso de aplicação, onde exploramos a forma como a implementação de soluções inovadoras, tais como bombas de purga automáticas e sistemas de controlo avançados, ajudaram a transformar as operações de uma fábrica de lacticínios.
Descubra como estas melhorias não só resolveram problemas críticos, como também geraram poupanças anuais de $22.000, com um período de recuperação de apenas dois anos.
Continue a ler para conhecer os desafios, as soluções implementadas e os resultados alcançados neste exemplo inspirador de otimização industrial.
Situação
Uma empresa líder no sector dos lacticínios, localizada na Carolina do Norte, EUA, operava como uma unidade de média escala especializada na produção de leite pasteurizado, gelados e outros produtos lácteos. A fábrica foi inicialmente projectada para lidar com uma capacidade limitada, mas ao longo do tempo registou um crescimento significativo nos volumes de produção devido ao aumento da procura no mercado regional.
Este crescimento exponencial foi um fator de sucesso para a empresa, mas também expôs limitações significativas nos processos operacionais. Com uma única caldeira para fornecer vapor a todas as aplicações críticas (incluindo pasteurização, sistemas de limpeza no local (CIP) e outros processos térmicos), a fábrica enfrentou problemas relacionados com o controlo de custos e a sustentabilidade operacional.
Os dados demográficos e as caraterísticas do mercado da empresa também desempenharam um papel importante. Operando num ambiente competitivo na Carolina do Norte, onde a eficiência e a sustentabilidade são factores chave para manter a rentabilidade, a empresa identificou que os seus sistemas de vapor e condensados não eram os melhores e necessitavam de melhorias significativas.
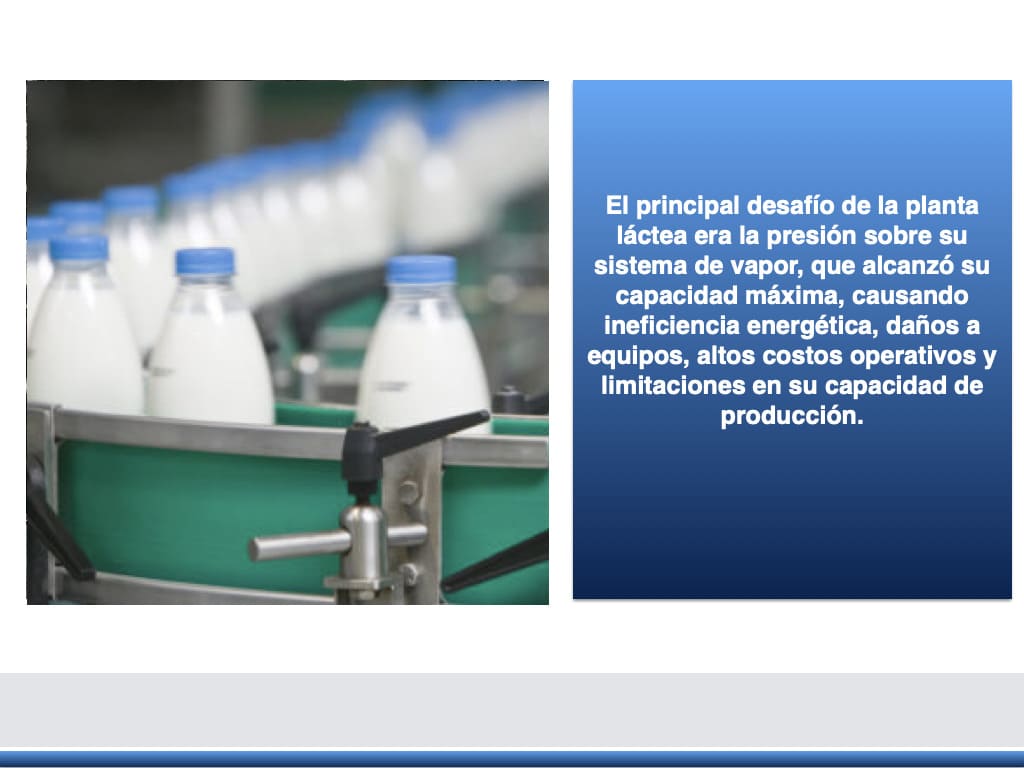
Problemas e desafios
O principal desafio da empresa era a pressão crescente no seu sistema de vapor, que tinha atingido a sua capacidade máxima devido ao aumento da produção. Isto resultou numa série de problemas operacionais:
- Custos excessivos: As despesas com produtos químicos para o tratamento da água, o combustível e o consumo de água de compensação dispararam devido às ineficiências do sistema.
- Ineficiência do sistema de condensação: Os sistemas de condensados dependiam de bombas eléctricas que sofriam de problemas de cavitação e não devolviam os condensados de forma eficiente para a caldeira, o que aumentava o desperdício de energia.
- Danos no equipamento: Os permutadores de calor utilizados nas aplicações de pasteurização e CIP eram frequentemente danificados devido a um controlo de temperatura deficiente e a uma remoção inadequada dos condensados.
- Estagnação do processo: Alguns permutadores de calor sofreram "estagnação" de condensado que interrompeu a produção e os ciclos de limpeza, afectando a eficiência global do processo.
Estes problemas não só representavam custos de exploração elevados, como também ameaçavam limitar a capacidade de produção futura e a capacidade da fábrica para competir no mercado.
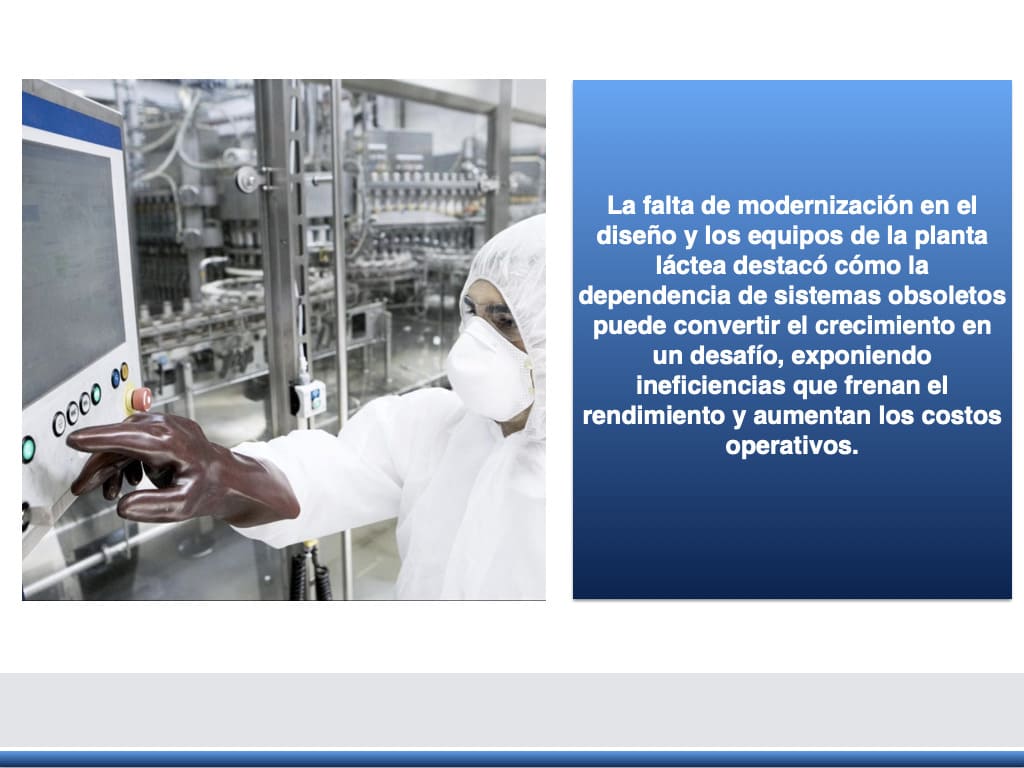
Razões
As razões que contribuíram para estes problemas estavam principalmente relacionadas com a conceção e o estado dos sistemas existentes:
- Dependência de uma única caldeira: A fábrica utilizava uma única caldeira a funcionar perto da sua capacidade máxima, não deixando espaço para lidar com cargas adicionais sem comprometer o desempenho.
- Sistemas de controlo obsoletos: As electroválvulas de vapor funcionavam num modo on/off que não permitia um controlo preciso da temperatura, o que contribuía para o desgaste dos permutadores de calor.
- Purgadores de vapor ineficientes: Alguns purgadores não retornavam o condensado para a caldeira, enquanto outros não conseguiam suportar as altas temperaturas, levando a perdas de energia e problemas de manutenção.
- Baixo rendimento das bombas eléctricas: As electrobombas utilizadas para o retorno dos condensados eram insuficientes para o caudal necessário e sofriam de cavitação frequente e de problemas de manutenção.
A combinação destes factores criou um sistema de vapor e condensados ineficiente, dispendioso e insustentável.
Capacidades técnicas
Para resolver os problemas identificados, era necessário implementar uma abordagem técnica sólida que incluísse as seguintes capacidades:
- Diagnóstico completo do sistema: Realizar uma auditoria detalhada dos sistemas de vapor e condensados para identificar áreas de melhoria e conceber soluções específicas.
- Capacidades de engenharia personalizadas: Desenvolver e instalar sistemas para atender às necessidades exclusivas da fábrica, como módulos de purgadores de bombas montados em skids.
- Soluções de controlo avançadas: Substituir as válvulas solenóides on/off por sistemas que permitam um controlo mais preciso da temperatura e do fluxo de condensado.
- Sistemas de condensação robustos: Implementar purgadores de bomba capazes de suportar temperaturas elevadas e assegurar um retorno eficiente dos condensados à caldeira.
- Minimização das interrupções: Conceber soluções que se integrem facilmente nos processos existentes sem afetar o funcionamento contínuo da fábrica.
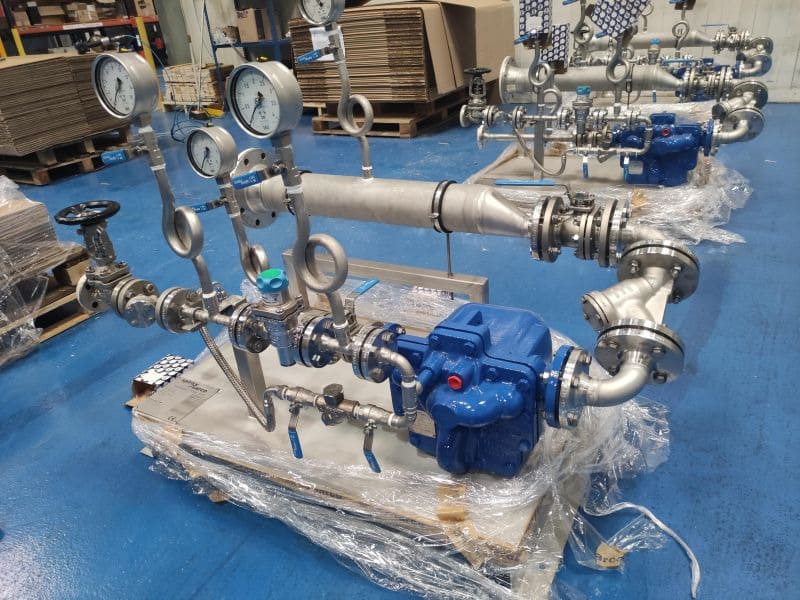
A solução
A Spirax Sarco forneceu e instalou uma solução abrangente que resolveu os problemas existentes na fábrica:
- Instalação de sistemas automáticos de armadilhas para bombas (APT): As bombas eléctricas defeituosas foram substituídas por sistemas APT14 nos permutadores de calor das aplicações de pasteurização e CIP. Estes sistemas garantiram uma remoção eficiente dos condensados e evitaram a estagnação do processo.
- Configuração dos módulos montados em skid: Os sistemas de bombas de purga foram instalados como pacotes montados em skids, o que simplificou a instalação e minimizou as interrupções na produção.
- Otimização do controlo da temperatura: As válvulas solenóides de regulação do vapor foram substituídas por sistemas que permitem um controlo mais preciso da temperatura, melhorando o desempenho dos permutadores de calor.
- Alargar a solução: Com base nos benefícios iniciais, foram instalados sistemas semelhantes noutras aplicações, como a máquina de lavar caixas e os permutadores de calor para a produção de sumo de laranja e leite, que também enfrentavam problemas de estagnação e ineficiência.
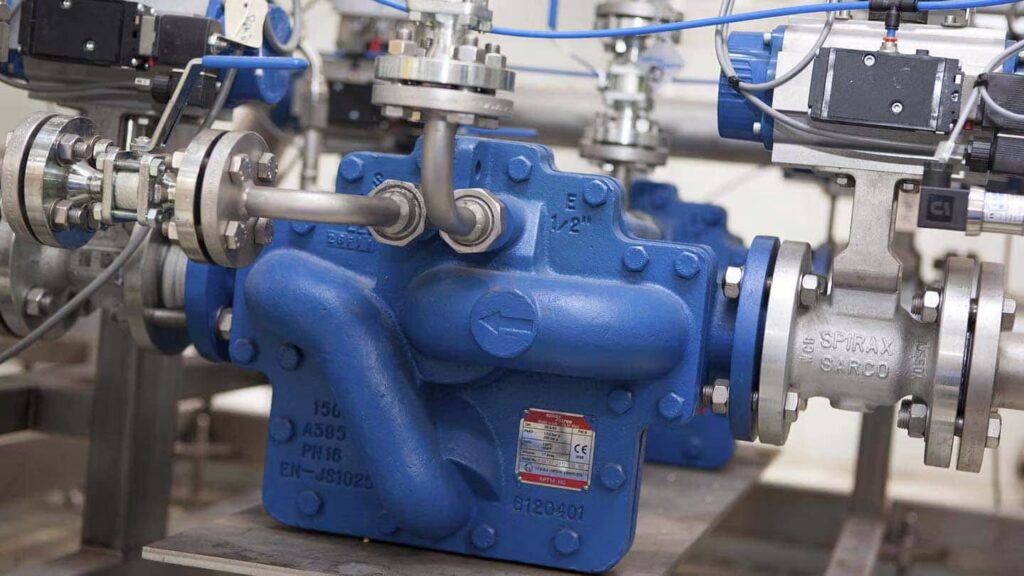
Resultados
A implementação das soluções propostas gerou resultados mensuráveis e melhorias significativas no funcionamento da fábrica:
- Poupança de energia: Foram conseguidas poupanças anuais de $22.000 nas aplicações de pasteurização e CIP devido à redução do consumo de energia e de água de compensação.
- Período de recuperação curto: O retorno do investimento foi estimado em cerca de dois anos, o que torna a solução altamente rentável.
- Redução dos custos de exploração: As despesas de manutenção e de produtos químicos para o tratamento da água foram reduzidas devido à melhoria da eficiência do sistema.
- Aumento da fiabilidade do sistema: Os problemas frequentes de cavitação e manutenção das bombas eléctricas foram eliminados, reduzindo significativamente o tempo de paragem do processo.
- Melhoria da sustentabilidade: Ao devolver o condensado à caldeira e reduzir as emissões de vapor flash, a fábrica melhorou a sua pegada ambiental e avançou para operações mais sustentáveis.
- Capacidade de expansão: A otimização do sistema de vapor permitiu que a fábrica suportasse volumes de produção mais elevados sem a necessidade de investir numa caldeira adicional.
Quer reduzir custos, melhorar a eficiência e aumentar a sustentabilidade da sua fábrica? Este estudo de caso demonstra como uma fábrica de lacticínios optimizou o seu sistema de vapor e condensados, resolvendo problemas críticos e conseguindo poupanças anuais de $22.000 com um período de retorno de apenas dois anos.
Não fique para trás. Explore as soluções implementadas, os desafios ultrapassados e os resultados alcançados para aplicar estas estratégias nas suas próprias operações. Contactar um consultor da Spirax Sarco
Deixe uma resposta